CNC Machining in Copper
Excellent thermal and electrical conductivity. Copper offers superior thermal and electrical conductivity, making it ideal for busbars, wire connectors, and other electrical applications. Copper has a distinctive glossy reddish-orange appearance and excellent corrosion resistance.
Order CNC Machined Copper Parts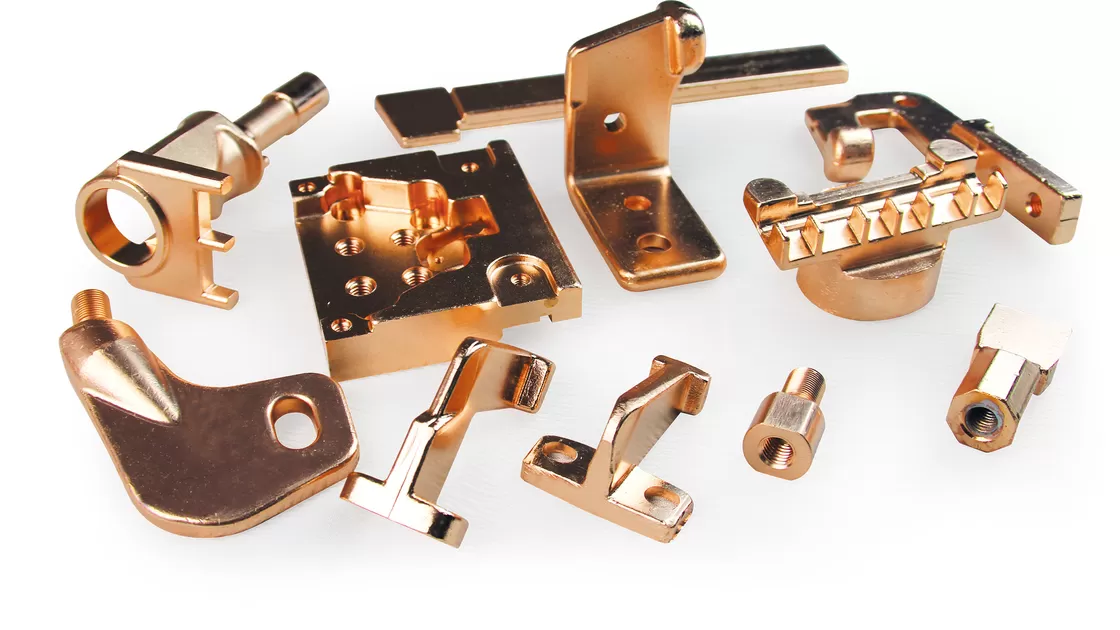
Custom Copper Parts
Copper is a versatile and valuable engineering material offering exceptional thermal and electrical conductivity, corrosion resistance, and antimicrobial properties. With its distinctive reddish-orange appearance, copper is a popular choice for both functional and decorative applications across various industries.
BZ Metal Products' CNC machining services deliver precision copper components with tight tolerances and excellent surface finishes. Our capabilities include both 3-axis and 5-axis CNC milling and turning, allowing us to create complex geometries for your most demanding applications in electrical engineering, plumbing, renewable energy, and architectural industries.
Superior Conductivity
Second only to silver in electrical conductivity, copper is the preferred material for electrical components, busbars, and heat sinks
Corrosion Resistant
Natural resistance to corrosion in most environments, forming a protective patina that prevents further degradation
Antimicrobial Properties
Natural ability to kill bacteria, viruses, and other pathogens, making it excellent for medical and public health applications
CNC Machining Copper Materials
BZ Metal Products offers high-quality copper alloys for CNC machining. Our copper materials provide excellent electrical and thermal conductivity, corrosion resistance, and aesthetic appeal for your precision components.
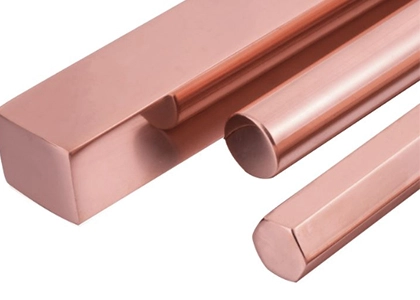
Copper C110
CU ETP | Electrolytic Tough Pitch Copper
Copper C110 is 99.90% pure copper with excellent electrical and thermal conductivity, good corrosion resistance, and high ductility. Ideal for electrical applications requiring maximum conductivity.
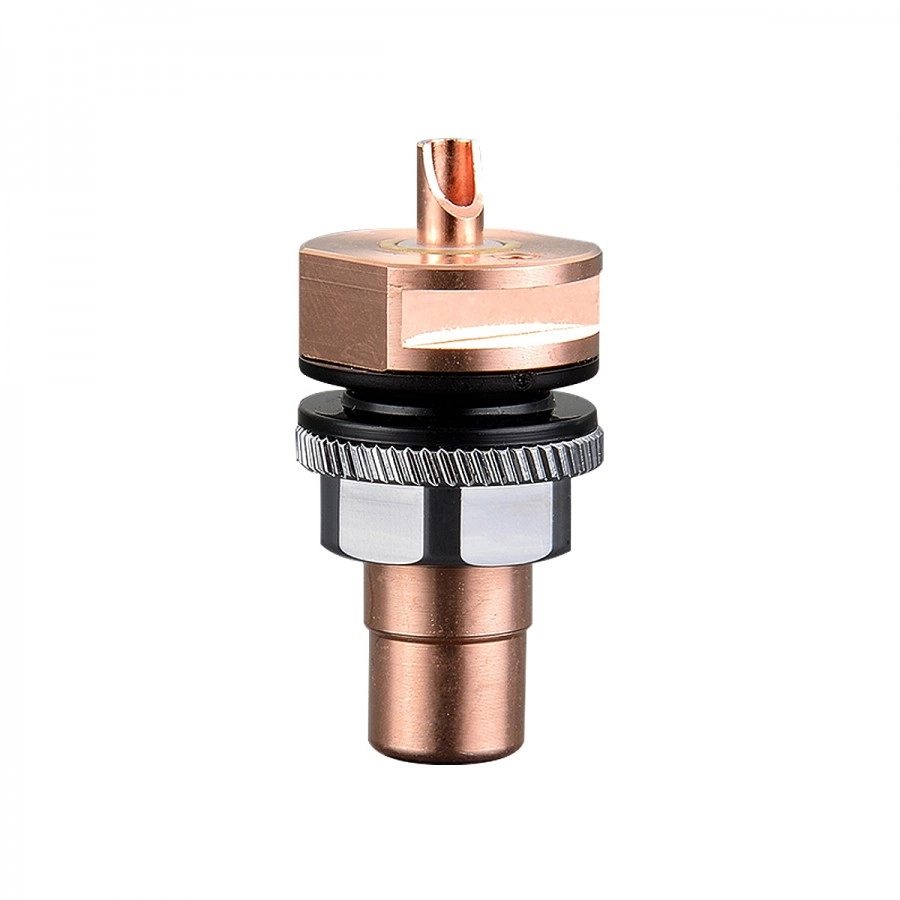
Copper C101
CU OFE | Oxygen-Free Electronic Copper
Copper C101 is 99.99% pure oxygen-free copper with superior electrical conductivity, excellent corrosion resistance, and enhanced ductility. Perfect for high-precision electronic and vacuum applications.
Additional Copper Grades Available by Request
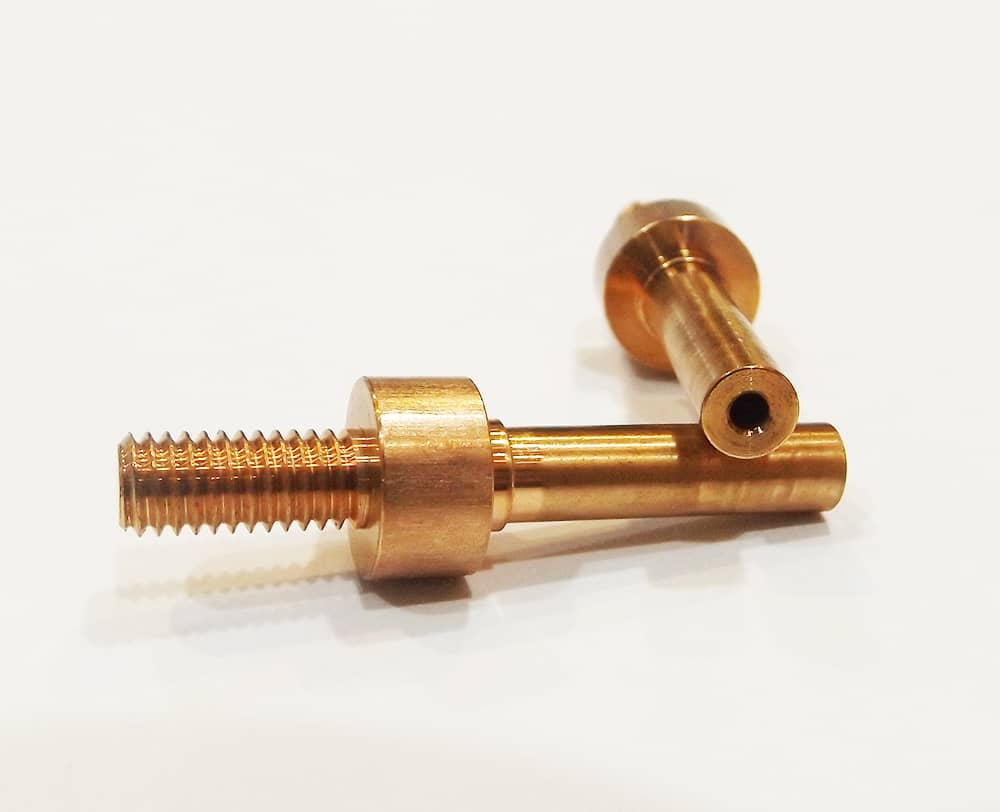
Tellurium Copper C145
Enhanced machinability with excellent electrical properties
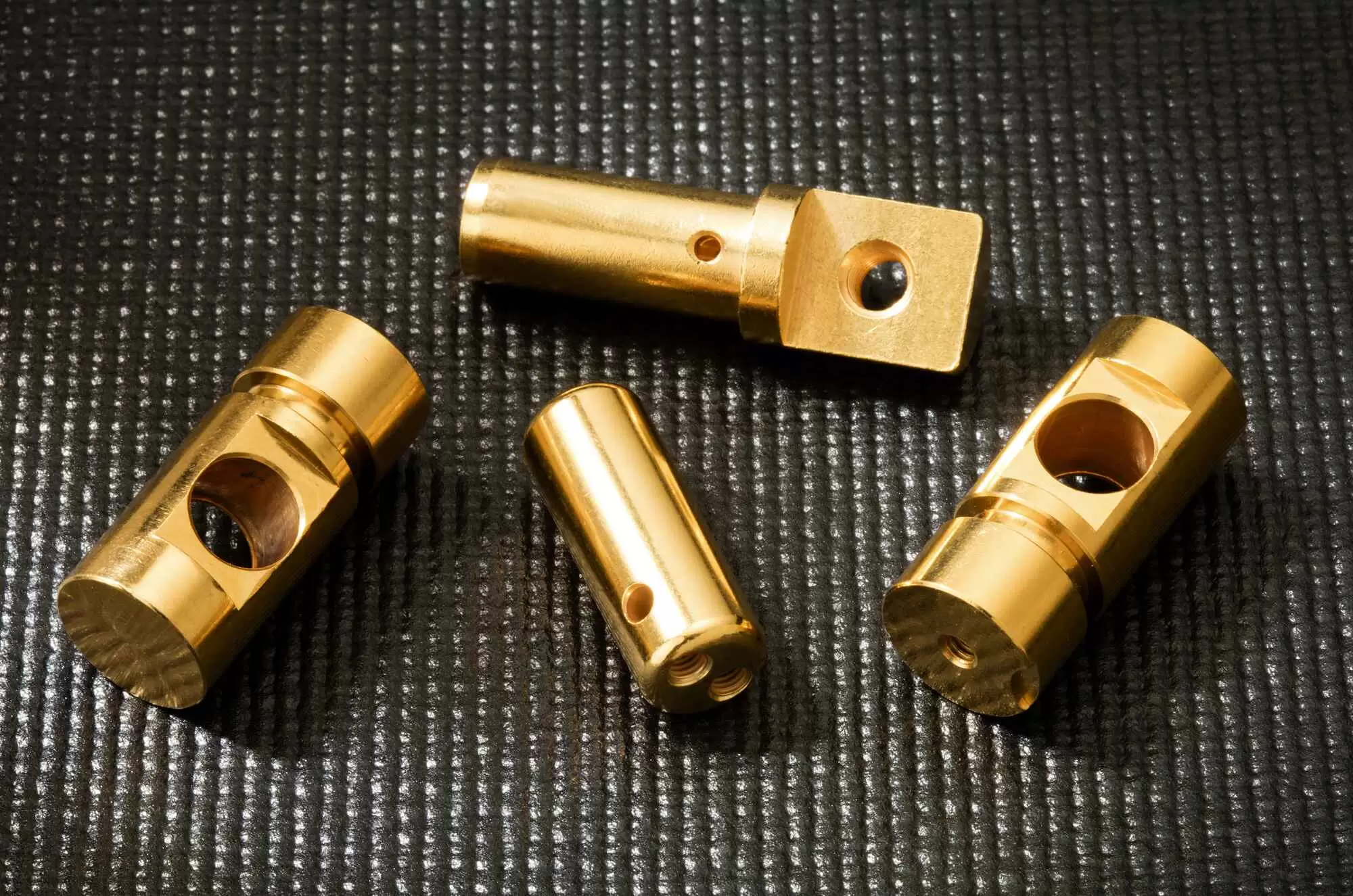
Beryllium Copper C172
High strength, hardness, and excellent spring properties
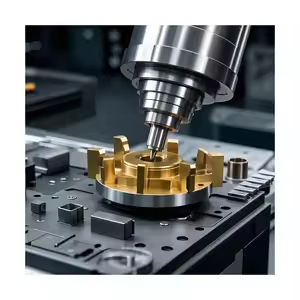
Commercial Bronze C220
90% copper, 10% zinc with improved strength and machinability
Copper Properties Overview
Property | Copper C110 | Copper C101 | Units |
---|---|---|---|
Tensile Strength | 220-250 | 220-240 | MPa |
Yield Strength | 69-100 | 60-90 | MPa |
Elongation | 45-55 | 50-60 | % |
Hardness (Brinell) | 40-45 | 35-45 | HB |
Modulus of Elasticity | 117 | 117 | GPa |
Machinability (relative to free-cutting brass) | 20 | 20 | % |
Property | Copper C110 | Copper C101 | Units |
---|---|---|---|
Density | 8.94 | 8.94 | g/cm³ |
Melting Point | 1083 | 1083 | °C |
Thermal Conductivity | 385-391 | 391-398 | W/m·K |
Electrical Conductivity | 100-101 | 101-102 | % IACS |
Coefficient of Thermal Expansion | 17.7 | 17.7 | μm/m·K |
Specific Heat Capacity | 385 | 385 | J/kg·K |
Element | Copper C110 | Copper C101 |
---|---|---|
Copper (Cu) min | 99.90% | 99.99% |
Oxygen (O) | 0.02-0.04% | <0.0005% |
Phosphorus (P) max | - | 0.0003% |
Lead (Pb) max | 0.005% | 0.0005% |
Bismuth (Bi) max | 0.001% | 0.0001% |
Total Impurities max | 0.10% | 0.01% |
Characteristics & Applications
Electrical & Thermal Conductivity
Copper's exceptional electrical and thermal conductivity makes it the material of choice for electrical components, busbars, heat exchangers, and thermal management applications. Only silver exceeds copper's conductivity, but at a significantly higher cost.
Corrosion Resistance
Copper naturally resists corrosion in many environments, including freshwater, saltwater, soil, and most non-oxidizing acids. Over time, it forms a protective patina that prevents further corrosion, making it ideal for long-term applications in harsh environments.
Machinability Considerations
While pure copper has relatively poor machinability (about 20% compared to free-cutting brass), our CNC machining expertise allows us to achieve excellent results. For applications requiring improved machinability, we recommend considering tellurium copper (C145) which has enhanced machining characteristics.
Antimicrobial Properties
Copper surfaces naturally kill bacteria, viruses, and fungi, making copper components ideal for healthcare settings, public spaces, and any application where reducing pathogen transmission is important. This inherent property has made copper increasingly popular for door hardware, fixtures, and touch surfaces.
Copper CNC Machining Services
BZ Metal Products offers complete copper CNC machining services from prototyping to production. Our expertise in working with copper allows us to produce complex components with excellent precision and surface finish, despite the unique machining challenges this material presents.
Expert Copper Machining
Our team specializes in the unique challenges of copper machining, including its tendency to work harden and its high thermal conductivity. We use specialized tooling, optimized cutting parameters, and effective cooling strategies to achieve excellent results with this demanding material.
Complex Geometries
We utilize advanced 3-axis and 5-axis CNC milling equipment to produce copper components with complex geometries, tight tolerances, and excellent surface finishes. Our capabilities extend from simple parts to intricate designs with challenging features.
Finishing Options
We offer a variety of surface finishing options for copper components including polishing, brushing, patination, and various protective coatings. These finishes enhance both the appearance and performance of your copper components while providing additional protection when needed.
Our Copper Machining Process
From design to delivery, our streamlined process ensures high-quality copper components that meet your exact specifications. We focus on efficiency and quality at every stage of production, with special attention to the unique requirements of copper machining.
Design Review & Optimization
We carefully review your design for manufacturability, with special attention to copper's specific characteristics. Our engineers may suggest design modifications to enhance performance, reduce costs, or improve machinability.
Material Selection
We help you select the optimal copper grade based on your application requirements, balancing factors such as electrical conductivity, thermal performance, corrosion resistance, and machinability.
CNC Programming
Our programmers create optimized toolpaths specifically for copper machining, accounting for the material's unique properties. We carefully select cutting speeds, feed rates, and tool engagement to prevent work hardening and achieve excellent surface finishes.
Precision Machining
Using specialized cutting tools and cooling strategies, we carefully machine your copper components to precise specifications. Our expert machinists monitor the process closely to ensure optimal results.
Deburring & Cleaning
We meticulously deburr and clean all copper components to remove any machining artifacts and prepare the parts for finishing or assembly. This step is critical for components used in electrical applications.
Surface Finishing
If specified, your copper parts receive surface finishing treatments to enhance appearance, conductivity, or provide protection against oxidation and tarnishing.
Quality Inspection
All copper components undergo thorough inspection to verify dimensions, tolerances, and surface quality before shipping. We use precision measuring equipment including CMMs for critical features.
CNC Machining Specifications
Price
Premium pricing reflecting copper's value and machining complexity
Lead Time
Typically 7-14 days depending on complexity and finishing requirements
Wall Thickness
Minimum 0.75 mm recommended for structural integrity
Tolerances
Standard: ±0.125mm (±0.005″), Precision: ±0.05mm (±0.002″)
Max Part Size
400 x 300 x 150 mm for standard parts, larger dimensions available on request
Surface Finish
As machined, polished, brushed, patinated, or coated
Common Applications for Copper Components
Copper CNC machined parts are ideal for a wide range of applications across multiple industries. Here are some common uses for our precision copper components:
Electrical
- Busbars and conductors
- Terminal blocks
- Connectors and contacts
- Switch components
Thermal Management
- Heat sinks
- Cold plates
- Heat exchangers
- Cooling blocks for electronics
RF and Microwave
- Waveguides
- Resonators
- RF cavities
- Antenna components
Medical
- Antimicrobial fixtures
- MRI components
- Oxygen systems
- Surgical instruments
Plumbing & Fluid Handling
- Custom fittings
- Manifolds
- Valves and components
- Fluid distribution systems
Renewable Energy
- Solar panel components
- Wind turbine electrical parts
- Battery connection systems
- Thermal management systems
Industries We Serve
Electronics & Semiconductor
Power Generation & Distribution
Telecommunications
Aerospace & Defense
Scientific & Laboratory
Architectural & Decorative
Frequently Asked Questions
Get answers to common questions about copper CNC machining. If you can't find what you're looking for, please contact our engineering team for assistance.
What are the key properties that make copper ideal for my application?
Copper is valued for several key properties: excellent electrical conductivity (second only to silver), superior thermal conductivity, good corrosion resistance, antimicrobial properties, and recyclability. It's ideal for applications requiring heat transfer, electrical conduction, or antimicrobial surfaces. The specific copper alloy selected can enhance certain properties for specialized applications. Our engineers can help you determine if copper is the right material for your specific requirements.
What are the differences between copper grades, and how do I choose?
Different copper grades offer varying balances of properties:
- C110 (Electrolytic Tough Pitch): Highest electrical conductivity, excellent thermal conductivity, but lower machinability
- C101 (Oxygen-Free): High conductivity with improved weldability and ductility
- C145 (Tellurium Copper): Better machinability while maintaining good conductivity
- C172 (Beryllium Copper): Higher strength and hardness with moderate conductivity
- C220 (Commercial Bronze): Better corrosion resistance with moderate conductivity
The choice depends on your application requirements. Our team can help you select the optimal grade based on factors like electrical/thermal needs, mechanical requirements, environment exposure, and cost considerations.
What tolerances can you achieve with copper CNC machining?
With copper CNC machining, we can achieve standard tolerances of ±0.125mm (±0.005″) and precision tolerances of ±0.05mm (±0.002″) for critical features. These tolerances may vary based on part geometry, size, and specific copper alloy used. Copper's thermal expansion coefficient (higher than many other metals) must be considered for tight tolerance applications, especially when operating temperatures vary significantly. Our experienced machinists use specialized techniques to account for these properties, ensuring accurate and consistent results.
What surface finishes are available for copper components?
We offer several surface finishes for copper components:
- As-machined: Standard finish directly from the CNC process
- Polished: Mirror-like finish for enhanced appearance or reduced friction
- Brushed: Directional satin finish that reduces visible fingerprints
- Patinated: Controlled oxidation for decorative antique appearance
- Clear coated: Protective layer to prevent tarnishing and oxidation
- Plated: Additional metal layers for enhanced properties or appearance
The optimal finish depends on your application's functional requirements and aesthetic preferences. For electrical components, we can also discuss specialized finishes to optimize conductivity at connection points.
What design considerations are important for copper CNC machining?
When designing parts for copper CNC machining, consider these factors:
- Wall thickness: Maintain minimum wall thickness of 0.75mm to prevent deformation
- Feature complexity: Design with tool accessibility in mind; avoid extremely deep slots or internal features if possible
- Corner radii: Include small radii in internal corners (min. 0.5mm) for better machinability
- Thermal considerations: Account for copper's high thermal conductivity and expansion in designs with tight tolerances
- Surface area: Large flat surfaces may require additional support during machining to prevent deflection
- Thread design: Copper threads can wear more quickly; consider thread strength requirements
Our engineering team can review your designs and provide feedback to optimize them for copper CNC machining, potentially saving time and reducing costs.
Get Your Copper Parts Into Production
Ready to leverage copper's excellent properties for your next project? BZ Metal Products offers expert CNC machining services for all copper grades. From prototypes to production runs, we ensure high-quality parts that meet your exact specifications.
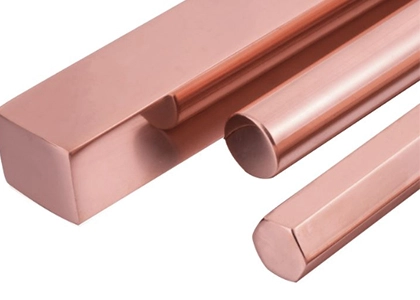